CNC Bending
CNC bending, also known as computer numerical control bending, is a metal forming process that utilizes computer-controlled machines to bend sheet metal or other ductile materials into desired shapes. It offers precise and efficient bending capabilities, allowing for complex geometries and accurate bending angles. CNC bending is widely used in industries such as automotive, aerospace, electronics, and manufacturing.
Here’s an overview of the CNC bending process:
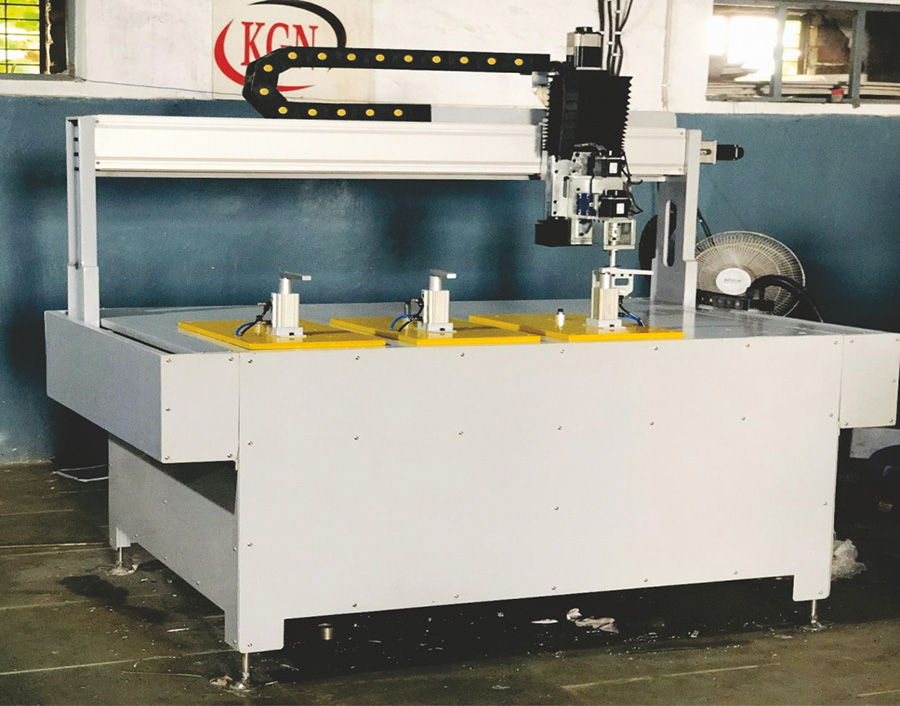
Design and Programming: The first step in CNC bending is to design the desired shape or component using computer-aided design (CAD) software. Once the design is finalized, the bending parameters, such as bend angles, tooling requirements, and sequencing, are programmed into the CNC bending machine using computer-aided manufacturing (CAM) software.
Material Selection and Preparation: Choose the appropriate sheet metal or ductile material for the bending process, considering factors such as thickness, ductility, and the required properties of the final product. The material is then prepared by cleaning, deburring, or flattening as necessary.
Tooling Setup: Install the appropriate tooling, such as a punch and die set, into the CNC bending machine. The tooling is selected based on the desired bending angle, material thickness, and part geometry. Tooling options may include V-dies, U-dies, or custom tooling specific to the bending requirements.
Workpiece Placement and Fixturing: Position the workpiece, typically a flat sheet of material, onto the bending machine’s work surface or bed. Use fixtures or clamps to secure the workpiece in place, ensuring proper alignment with the machine’s reference points or stops.
CNC Bending Process: Activate the CNC bending machine and initiate the bending process. The machine’s computer control system precisely coordinates the movement of the bending tools and workpiece, controlling the bending angle, tool position, and other parameters defined in the programming.