Hose Sizing & Cooling
When it comes to fluid handling and cooling applications, selecting the right hose size and implementing effective cooling solutions are crucial. Here’s an overview of hose sizing considerations and cooling options to optimize your system:

Hose Sizing:
Fluid Flow Rate: Determine the required flow rate of the fluid through the hose. This depends on factors such as the application, desired velocity, and system requirements. Higher flow rates generally require larger hose sizes to minimize pressure drop.
Hose Diameter: Consider the inside diameter (ID) of the hose. A larger ID allows for greater flow capacity. It’s essential to match the hose diameter with the required flow rate to prevent excessive pressure drop and ensure efficient fluid transfer.
Pressure Rating: Ensure that the selected hose has a pressure rating suitable for your application. It should withstand the maximum operating pressure without compromising safety or performance.
Temperature Range: Verify that the hose can handle the temperatures of the fluid and environment it will be exposed to. Some applications may require hoses specifically designed for high-temperature or cryogenic environments.
Cooling Solutions:
Heat Exchangers: Implementing heat exchangers can effectively cool fluids in various applications. They transfer heat from the fluid to a cooling medium, such as air or water, using conductive or convective methods. Select a heat exchanger type (e.g., shell and tube, plate, or finned) based on your cooling requirements and available resources.
Radiators: Radiators are commonly used in automotive and industrial applications to cool engine coolant or other fluids. They employ a combination of convection and radiation to dissipate heat. Proper sizing and placement of radiators are crucial to ensure efficient cooling.
Cooling Towers: Cooling towers are widely used for large-scale cooling applications, such as HVAC systems or industrial processes. They use evaporation and air circulation to remove heat from water or other fluids. Cooling towers are available in different designs, including cross-flow and counter-flow configurations.
Heat Sinks: Heat sinks are commonly used to cool electronic components. They maximize the surface area exposed to the air, enhancing heat dissipation through convection. Heat sinks come in various shapes and materials, such as aluminum or copper, depending on the application requirements.
Fluid Coolers: Fluid coolers, such as air-cooled or water-cooled chillers, are efficient options for cooling large volumes of fluid. They utilize refrigeration or cooling coils to remove heat from the fluid, providing precise temperature control.
Fans and Blowers: Fans and blowers are used to enhance airflow and improve heat dissipation. They can be integrated with other cooling systems or employed as standalone solutions in certain applications.
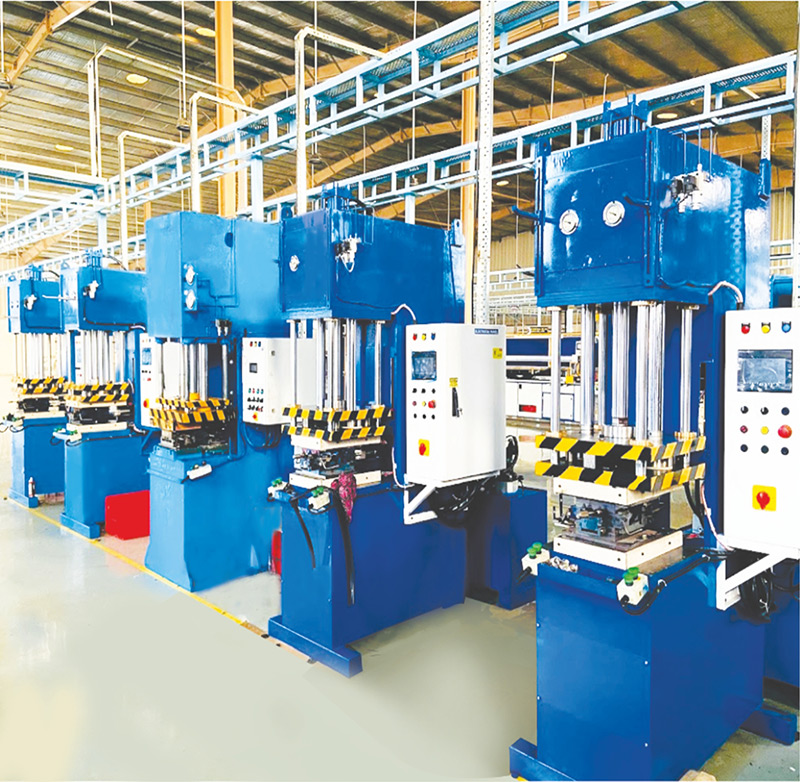